Environmental Engineering Defined
What is environmental engineering? Do you pick up litter?” To which you probably know the answer to the second question is a definite “NO!!!”. However, you may not know the answer to the first question.
Encyclopedia
According to Britannica (https://www.britannica.com), “environmental engineering is the development of processes and infrastructure for the supply of water, the disposal of waste, and the control of pollution of all kinds.” These endeavours protect public health by preventing disease transmission, and they preserve the quality of the environment by averting the contamination and degradation of air, water, and land resources.
Wikipedia
According to Wikipedia (https://en.wikipedia.org), environmental engineering is “a professional engineering discipline that takes from broad scientific topics like chemistry, biology, ecology, geology, hydraulics, hydrology, microbiology, and mathematics to create solutions that will protect and also improve the health of living organisms and improve the quality of the environment.” This definition is very similar to the one above. And note that both accurately define environmental engineering.
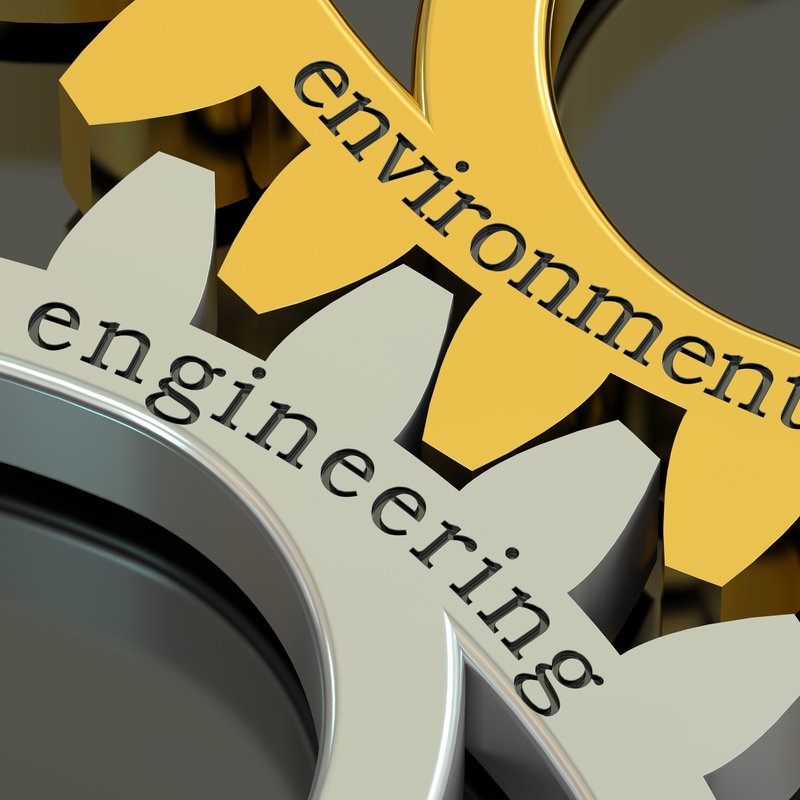
Environmental Engineering Evolution
Historically, sanitary civil engineers did environmental engineering like work. However, they be-came known as environmental engineers in the mid-1960’s with the recognition of pollution and the outcries to clean it up. As a result, scientists and engineers answered the call. Firstly, they addressed water pollution. Next, they turned to air pollution. Finally, they focused on land pollution. They followed three landmark federal laws: the Clean Water Act (1972), the Clean Air Act (1970), and the Comprehensive Environmental Response, Compensation, & Liability Act (1980). It is extremely impressive that the U.S. Congress passed these laws so quickly! And what they did was create the need for environmental regulations, permits, and agencies to accomplish the mission.
Agencies
Federal
Agencies, you ask? Firstly, let’s start at the top – the U.S. Environmental Protection Agency (https://www.epa.gov) came out of Reorganization Plan No. 3 calling for the establishment of that agency. That was an executive order which President Richard M. Nixon signed on July 9, 1970.
The EPA began operation on December 2, 1970. Wow, things seemed to move quickly fifty years ago!
State & Local
Once the EPA began publishing regulations to clean up the environment, they worked in cooperation with states to form departments or to use existing departments to implement the regulations. And so, state environmental departments formed to clean up the environment across each state. Cities and counties formed pollution control departments and divisions. Some health departments took on the responsibility.
EPA provided funding. States, counties, and cities needed it to comply. That was critical for projects such as new wastewater treatment plants. If the states did not enforce the environmental regulations, EPA would cut funding. And that meant jobs, worsening pollution, and outcries from the public. So there were many different incentives to comply.
Environmental Engineer’s Role
Formerly known as civil or sanitary engineers, environmental engineers came to the forefront. They assisted the various governmental agencies and the private sector with the environmental regulations.
Environmental Scientists
Environmental scientists and engineers began working together both in the government and private sectors. Their job? Ultimately, their job was to clean up the environment. Processes, equipment, and testing designs occurred in the areas of water, air, and land. And they are still at it today!
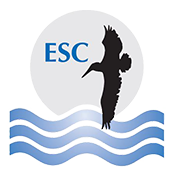
Conclusion
So there is a discussion of environmental engineering and what the environmental engineer’s role is! For further assistance, Environmental Safety Consultants (www.escflorida.com) is here. ESC holds a Florida environmental engineering license and has a Professional Engineer (P.E.) on staff. We have the credentials and experience to help you with your environmental engineering needs. We service Bradenton, Sarasota, St. Petersburg, Clearwater, Tampa, and Fort Myers. That includes Manatee, Pinellas, Hillsborough, Lee, and other counties from Pensacola (Escambia County) to Key West (Monroe County). So, Contact ESC and get a reply promptly!