What Toxic Mold Is
Mold or fungus are considered toxic if they cause one or more of the following health problems (www.cdc.gov). First, are burning or irritated eyes. Second, is runny nose, coughing, sneezing, wheezing, or a few other upper respiratory problems. Third, are headaches or fatigue. Fourth and last, are nausea and cognitive (brain) problems.Types That Are Toxic
Black Toxic Mold
Black toxic mold refers to a genus or type of mold called Stachybotrys. Further, it typically refers to a species called chartarum. But how did it get this famous reputation? Firstly, it is well known because of highly publicized court cases. Secondly, it was identified in a few highly publicized public health cases. And, finally, the media has given it a lot of attention. As a matter of fact, it received so much attention that some people believe it is the only toxic fungus. But, that is simply not true! Know the Mold myths and facts
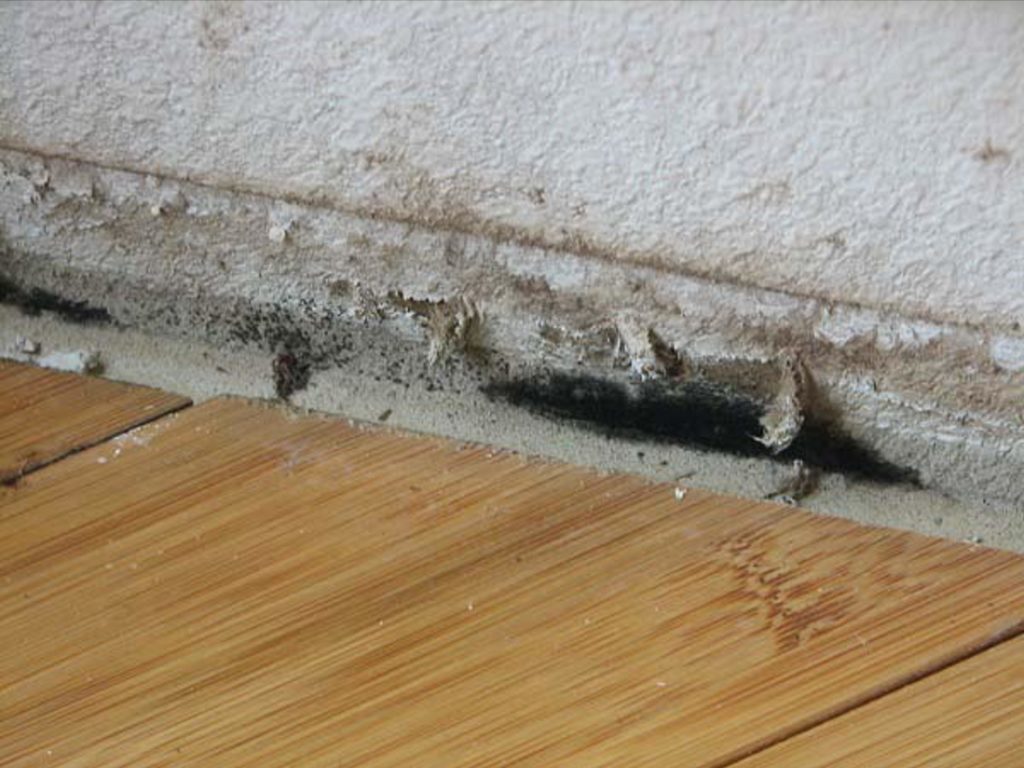
Other Mold that is Toxic
There are lots of other types or genera of mold which are toxic. This is well documented in the scientific literature. Some of the common ones are Penicillium, Aspergillus, Cladosporium, and Chaetomium. These grow actively both outside and inside buildings.
Causes of Toxicity
These types of mold are toxic because their spores, toxins, or chemicals can cause one or more of the health problems above. These problems may only involve one person in a building with hundreds of occupants. However, that one person experiences a definite health problem from the mold.
Why does that mold not cause a health problem for that same person outside the building? First, the mold population may be much larger inside. Second, there may not be enough fresh air ventilation inside. Third, the mold may be forming colonies on building materials or contents close to that person.
The difference inside is usually due to water. Firstly, the water can come from leaks around windows, doors, roofs, ice makers, and more. Secondly, the water can come from the air conditioner not running or malfunctioning. This can result in elevated humidity, condensate drain pan overflows, and more. Third, the water can come from floods. This may be from weather outside, toilets, and more. As a result of this water in a building, the mold grows and becomes much different in its population and the types.
Certain types of mold are toxic because they cause health problems for some people. There are many types of such mold in addition to the black mold. Water is usually the cause of the unique mold inside a building. In any event, ESC can help determine the cause and the solution for your toxic mold. Feel free to contact us today
Conclusions
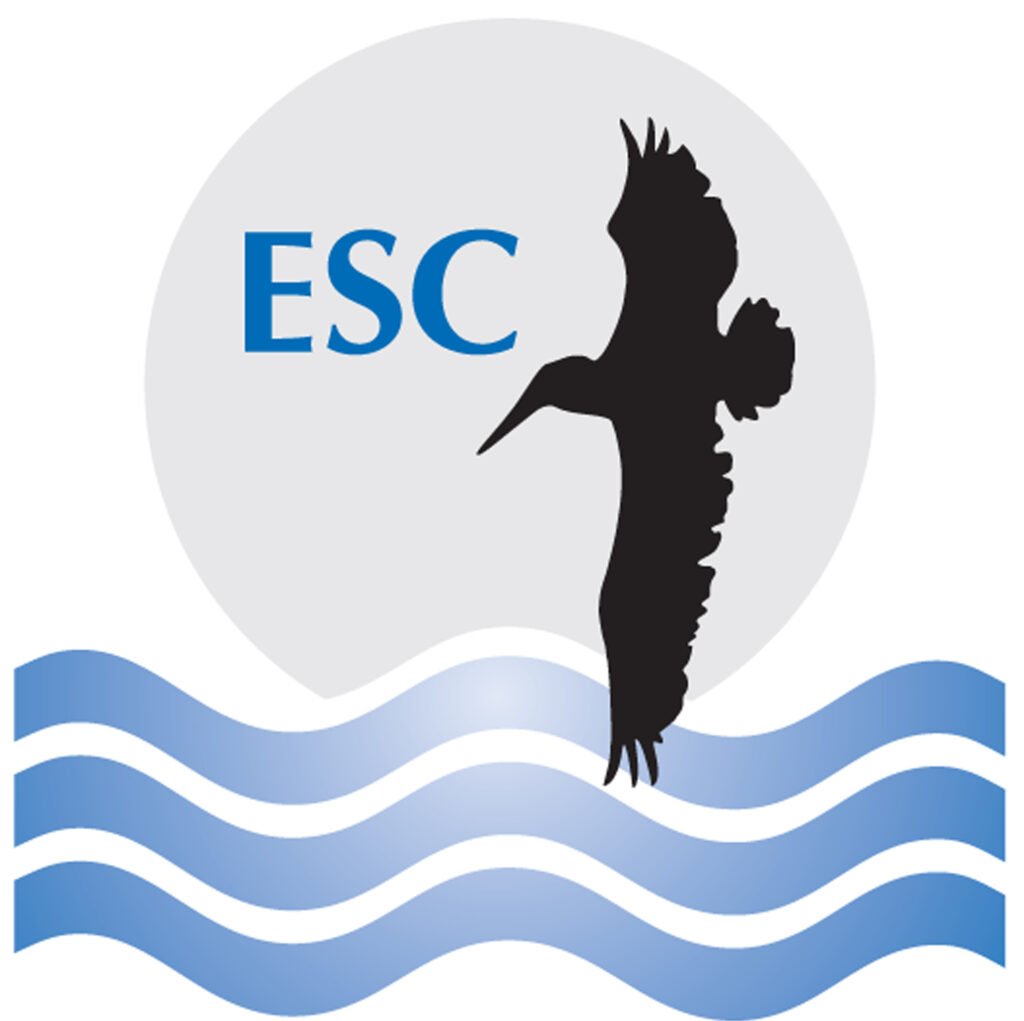
There are many types of mold which are toxic besides the well known black mold. ESC has Florida licensed mold assessors and a Certified Industrial Hygienist (CIH) on staff to help you. Contact ESC and get a reply promptly!
.